What are the implications of a specific type of copper wire used in electrical infrastructure? A particular copper wire configuration plays a crucial role in power transmission.
This copper wire, with its unique design and manufacturing process, is optimized for high-capacity electrical transmission and distribution. It is crafted for minimal resistance, ensuring efficient current flow. Examples of its application include high-voltage power lines, substations, and industrial wiring systems. Its superior conductivity, strength, and durability contribute to greater reliability and safety within electrical grids.
The efficiency and reliability achieved through this wire configuration are critical for maintaining stable power supply, supporting economic activities, and promoting sustainability. Its role in supporting communication systems and industrial operations also highlights its importance in the broader infrastructure. Technological advancements in wire manufacturing continue to refine these features, leading to improved performance and reduced energy loss. The focus on material science and engineering in designing this wire underlines its significance in modern infrastructure developments.
Moving forward, this article will delve into the specific technological aspects of this copper wire configuration, examining its material properties, manufacturing processes, and application standards.
The Wire KPKuang
Understanding the characteristics of the KPKuang wire is crucial for assessing its suitability in various electrical applications. Its composition, conductivity, and structural properties directly impact performance and safety. The following key aspects provide a comprehensive overview.
- Conductivity
- Strength
- Durability
- Manufacturing
- Diameter
- Insulation
- Application
- Safety Standards
These aspectsconductivity, strength, and durabilityare fundamental to the wire's performance. High conductivity minimizes energy loss, while robust strength ensures long-term reliability. Proper manufacturing processes and meticulous adherence to safety standards are crucial for producing a wire that meets specified electrical parameters. Wire diameter directly impacts current-carrying capacity. Insulation prevents short circuits, and suitable application ensures optimal performance within the intended environment. Examples include high-voltage transmission lines, where strength and conductivity are paramount, contrasted with the fine wire used in sensitive electronic components requiring precise diameter and insulation. This detailed examination of each aspect provides a nuanced understanding of KPKuang wire's applicability in various electrical settings.
1. Conductivity
The conductivity of KPKuang wire is a paramount consideration in its application. High conductivity directly impacts the wire's ability to transmit electrical current with minimal energy loss. This characteristic is critical for efficient power transmission and distribution, influencing operational costs and safety standards in various electrical systems. Analyzing this property delves into its fundamental role in determining the wire's performance and suitability for specific applications.
- Relationship to Material Composition
KPKuang wire's conductivity is primarily determined by the composition of its core material. High purity copper, often alloyed with other metals for specific properties, forms the basis of this conductivity. The purity and precise alloying composition directly affect the electron flow, thus influencing the overall conductivity of the wire. This intricate relationship between material composition and conductivity is critical for optimizing the wire's performance for various operational demands.
- Impact on Energy Loss
Lower resistance to current flow directly translates to lower energy loss during transmission. KPKuang wire, designed with high conductivity in mind, minimizes these losses. Reduced energy loss translates to improved efficiency and cost savings in large-scale power distribution systems. Minimizing transmission losses ensures the efficient delivery of electricity to consumers.
- Influence on Wire Sizing
The conductivity of KPKuang wire affects the required size for a given current carrying capacity. Higher conductivity permits the use of smaller wire gauges for the same current load, reducing material costs and the overall weight of the wiring system. This is particularly important for high-capacity transmission lines and complex electrical infrastructure.
- Impact on Safety Standards
High conductivity contributes to maintaining appropriate operating temperatures in electrical systems. Lower resistance facilitates faster and more efficient dissipation of heat, reducing the risk of thermal overload and associated safety hazards. This directly relates to the wire's adherence to safety regulations for various applications.
In summary, the conductivity of KPKuang wire is a defining feature that influences its suitability for different applications, impacting energy efficiency, operational costs, and safety standards. Optimizing conductivity in the manufacturing process is essential for ensuring reliable and cost-effective electrical infrastructure.
2. Strength
The strength of KPKuang wire is critical for its operational reliability and safety, particularly in high-stress environments. Its ability to withstand mechanical loads, both during installation and throughout its operational lifespan, is a key determinant in the long-term functionality of electrical systems. This robustness is essential in diverse applications, from high-voltage transmission lines to industrial equipment wiring.
- Tensile Strength and Elongation
The tensile strength of KPKuang wire defines its ability to resist pulling forces. High tensile strength is crucial for maintaining structural integrity under mechanical stress, ensuring that the wire does not stretch or break during installation or in use. The wire's elongation properties complement this, specifying how much it stretches before yielding under load. This balance between tensile strength and elongation is vital for maintaining wire integrity throughout its service life, especially under the unpredictable tensions within electrical infrastructure. Examples of this include the rigorous tests on the wire's ability to withstand the stresses in cable tray installations.
- Impact Resistance
Impact resistance assesses the wire's ability to withstand sudden, forceful impacts. This is critical in applications susceptible to accidental damage, like overhead transmission lines where the wire might be struck by debris or objects. Sufficient impact resistance reduces the likelihood of breakage and ensures the wire can withstand potentially damaging events in service. This contributes to both operational safety and the extended lifetime of the wiring system.
- Creep Resistance
Creep resistance in KPKuang wire refers to its ability to maintain its shape and strength over time when subjected to sustained loads or high temperatures. This is paramount in high-voltage applications where prolonged exposure to stress and heat is common. The wire's creep resistance prevents permanent deformation or weakening, ensuring long-term stability and reliability. This is evaluated by rigorous testing simulations over long periods at elevated temperatures, mirroring realistic service conditions.
- Environmental Factors
The wire's strength must also consider environmental factors like extreme temperatures, corrosive substances, or exposure to UV radiation. KPKuang wire's strength should be evaluated across a range of expected conditions to predict its durability over time. The impact of environmental degradation on the wire's mechanical properties needs careful consideration to assure performance throughout its intended service life. For example, rigorous tests are conducted on the wires ability to maintain its strength in environments containing common pollutants.
In conclusion, the strength characteristics of KPKuang wire are not just single properties but interconnected facets that collectively determine its suitability for diverse electrical applications. High tensile strength, impact resistance, and creep resistance, combined with resilience to environmental degradation, highlight the wire's robustness and underscore its importance in constructing dependable and long-lasting electrical infrastructure.
3. Durability
The durability of KPKuang wire is a critical factor influencing its suitability for various electrical applications. Durability encompasses the wire's ability to withstand environmental stresses, mechanical loads, and the effects of time. Its long-term performance directly impacts the reliability and lifespan of the electrical systems incorporating it. Weakening of the wire, either through corrosion or physical damage, can lead to significant disruptions, safety hazards, and costly repairs.
Factors affecting the durability of KPKuang wire include its material composition, manufacturing processes, and environmental conditions. High-purity copper, a key component, contributes to corrosion resistance. Sophisticated manufacturing techniques, ensuring consistent material properties and structural integrity, enhance the wire's ability to withstand mechanical stress. Exposure to corrosive elements, extreme temperatures, and prolonged UV radiation can diminish the wire's longevity. Real-world examples include the extended lifespan of overhead transmission lines utilizing KPKuang wire in climates with high humidity and the ability of underground cables to maintain conductivity despite prolonged soil interaction. Understanding these factors is essential for predicting the service life of wiring systems, facilitating proactive maintenance schedules, and preventing costly failures. Accurate assessments regarding the durability of the wire, when considering the intended operational environment, are crucial for successful deployment.
Ultimately, understanding the durability of KPKuang wire is vital for the design and implementation of reliable electrical infrastructure. A durable wire translates to reduced maintenance costs, minimized downtime, and enhanced safety for users. By considering the interplay between material properties, manufacturing processes, and environmental influences, engineers and technicians can select and maintain KPKuang wire to guarantee long-term performance within various electrical applications.
4. Manufacturing
The manufacturing process directly dictates the quality, consistency, and ultimately, the performance of KPKuang wire. Precise manufacturing methods ensure the wire meets stringent specifications, impacting factors such as conductivity, strength, and durability. Variations in manufacturing procedures can lead to significant disparities in the wire's overall effectiveness within electrical systems.
- Material Processing
The initial processing of raw copper is fundamental. Methods for refining and purifying copper affect its inherent conductivity. Impurities in the copper can negatively impact current flow, leading to increased resistance and energy loss. Rigorous quality control during material processing ensures a consistent supply of high-purity copper, crucial for the intended conductivity of KPKuang wire. The chosen refining and alloying processes determine the wire's electrochemical properties.
- Drawing and Shaping Processes
The drawing and shaping processes define the wire's final geometry. The precise control of wire diameter and cross-sectional area is crucial for achieving the required current-carrying capacity. Variations in these parameters can compromise the wire's ability to handle anticipated current loads. The precision achieved in the drawing process affects the wire's mechanical strength and ensures uniformity across the entire production run. Advanced drawing equipment allows for the creation of complex wire profiles, tailoring the wire's properties for specific applications.
- Quality Control Measures
Implementing rigorous quality control measures at various stages of manufacturing is vital for consistency. Testing procedures at each phase, such as conductivity testing and tensile strength evaluations, ensure the wire adheres to established standards. Consistent adherence to these procedures provides reliable assurance that the wire meets the intended specifications. Automated testing equipment is often integrated to maintain accuracy and consistency.
- Environmental Considerations
Modern manufacturing practices for KPKuang wire increasingly integrate environmental considerations. Minimizing energy consumption, reducing waste generation, and utilizing eco-friendly materials are integral to sustainable production. These environmentally conscious approaches demonstrate a commitment to responsible manufacturing, which is often a significant factor in selecting suppliers and manufacturers in the industry.
In summary, the manufacturing processes significantly influence the properties and reliability of KPKuang wire. Optimizing each stagefrom material processing to final quality checksis essential to ensure the wire performs as expected in diverse electrical applications. A robust and standardized manufacturing process is a key aspect of guaranteeing the long-term performance and safety of electrical systems incorporating KPKuang wire.
5. Diameter
The diameter of KPKuang wire is a critical parameter directly influencing its operational characteristics. Precise control over this dimension is essential for maintaining the wire's intended performance in various electrical applications. Different diameters accommodate different current carrying capacities and contribute to overall system efficiency and safety.
- Current-Carrying Capacity
A larger diameter wire typically possesses a higher current-carrying capacity. This is because a larger cross-sectional area allows for a greater flow of electrons with less resistance. This is crucial for high-current applications where thicker wires are necessary to prevent overheating and potential damage. Conversely, smaller diameter wires are suitable for lower current applications, where heat dissipation is less of a concern.
- Voltage Drop
The diameter of the wire directly impacts voltage drop across the conductor. Larger diameter wires offer lower resistance, leading to reduced voltage drop over longer distances. Minimizing voltage drop is essential in long-distance power transmission to ensure adequate voltage reaches the intended destination, preventing operational inefficiencies. The relationship between diameter and voltage drop is crucial for calculating the appropriate wire size for a specific application.
- Weight and Cost Considerations
Larger diameter wires have higher weight and material costs than smaller diameter ones. This economic aspect is often a significant consideration in system design, particularly in applications where weight or material expenses are important factors. The trade-off between electrical performance and cost must be evaluated meticulously during project planning and execution.
- Installation Considerations
The diameter of KPKuang wire influences installation feasibility. Thicker wires can be more challenging to maneuver and install, especially in confined spaces. The diameter must be carefully considered in relation to the space available and the necessary installation techniques. Choosing the correct diameter balances electrical performance with practical implementation.
In conclusion, the diameter of KPKuang wire is a multifaceted parameter impacting multiple aspects of its application. Careful consideration of current-carrying capacity, voltage drop, weight, and installation requirements is essential to ensure the optimal performance and economic viability of the electrical system. Selecting the appropriate diameter necessitates a comprehensive analysis of the specific application's needs to balance electrical efficiency with practical constraints.
6. Insulation
Insulation is an integral component of KPKuang wire, not merely an added layer, but a crucial determinant of its overall performance and safety. The effectiveness of the wire in electrical systems hinges on the quality and type of insulation. Proper insulation safeguards against short circuits, electrical shocks, and other hazards. It significantly impacts the wire's operational lifespan and reliability. A breakdown in insulation can lead to catastrophic consequences in electrical infrastructure, ranging from minor disruptions to major power outages and potential safety risks.
The insulation material selected for KPKuang wire dictates its operational characteristics in various environments. Different insulating materials possess distinct properties in terms of dielectric strength, temperature resistance, and chemical resistance. For example, in high-voltage applications, insulation with superior dielectric strength is crucial to prevent electrical breakdown, while in high-temperature environments, thermal stability is paramount. Moreover, the specific type of insulation influences the wire's ability to withstand exposure to moisture, chemicals, and other environmental factors. The chosen insulation plays a critical role in the wire's ability to meet stringent safety standards for electrical installations, emphasizing the importance of careful material selection and manufacturing processes. Examples include the use of specialized insulation in underground cables to resist moisture and the application of heat-resistant insulation in high-temperature environments, such as industrial settings.
Understanding the connection between insulation and KPKuang wire is essential for ensuring electrical safety and reliability. Appropriate insulation directly translates to minimized risk of electrical hazards, reduced maintenance requirements, and a prolonged lifespan for the electrical system. A comprehensive understanding of the insulation's properties, limitations, and potential weaknesses in the operational environment is crucial for selecting the right type of insulation for a particular application and designing systems with robust safety protocols. This crucial understanding informs the design and implementation of electrical systems, enabling professionals to prioritize safety, minimize potential risks, and maximize the long-term operational efficiency and safety of the infrastructure.
7. Application
The application of KPKuang wire directly dictates its relevance and impact within electrical systems. The specific use case determines the critical operational parameters needed, driving choices regarding material properties, manufacturing techniques, and design specifications. An inappropriate application can lead to underperformance, safety hazards, or premature failure. Conversely, a suitable application maximizes the wire's capabilities, enhancing efficiency and reliability. This connection between the wire and its intended use is crucial for a comprehensive understanding of its value in various electrical contexts.
Real-world examples highlight this interplay. In high-voltage transmission lines, KPKuang wire's strength and high conductivity are paramount. This ensures efficient power delivery over extended distances with minimal energy loss. In contrast, smaller diameter KPKuang wire, with its enhanced conductivity, finds application in densely populated urban areas, supporting intricate electrical networks and minimizing infrastructure footprint. Similarly, specialized insulation types, paired with specific wire diameters, are essential for underground cable applications, where resistance to moisture and environmental degradation are crucial. These diverse applications showcase how the precise matching of wire characteristics to the specific demands of a given project influences success and safety. Careful consideration of each application underscores the importance of understanding not only the wire's intrinsic properties but also the operational environment in which it will function.
Ultimately, understanding the application-specific requirements is fundamental for effective use of KPKuang wire. This knowledge allows for optimized selection and installation, minimizing risks and maximizing the wire's lifespan. Choosing the right application ensures the wire's full potential is realized, contributing to efficient and reliable electrical infrastructure. Furthermore, this understanding helps in anticipating potential challenges, allowing for proactive mitigation and the development of appropriate safety protocols specific to different applications, ultimately promoting a robust and secure electrical system.
8. Safety Standards
Adherence to safety standards is paramount in the application of KPKuang wire. These standards are not merely guidelines but essential safeguards for personnel and infrastructure. Compliance ensures the wire's safe operation within various electrical systems and minimizes the potential for hazards. Understanding these standards is crucial for reliable and safe electrical installations.
- Electrical Conductivity Testing
Rigorous testing of KPKuang wire's conductivity is essential. Accurate conductivity measurements verify the wire's ability to carry electrical current without excessive resistance. This testing, often conducted at various temperatures and environmental conditions, ensures that the wire consistently meets minimum required conductivity thresholds. Deviations from these standards could lead to significant energy loss, overheating, and potential fire hazards. The consistent application of this testing ensures the safety of the entire electrical system.
- Tensile Strength and Elongation Limits
Standards dictate the minimum tensile strength and elongation limits for KPKuang wire. These specifications ensure the wire can withstand mechanical stress during installation and throughout its operational lifespan without failure. Exceeding these limits can result in breakage, leading to disruptions in service, potentially causing power outages or creating safety hazards for individuals working around electrical infrastructure. Adhering to these standards is vital for long-term reliability and the prevention of accidents.
- Insulation Resistance Testing
Testing insulation resistance is a fundamental aspect of safety standards. Insulation integrity prevents short circuits and electrical shocks. These tests determine the insulation's ability to withstand electrical voltage without breakdown. Failures in insulation resistance can cause unexpected electrical arcs, posing significant risks to individuals and potentially causing fires or equipment damage. Compliance with insulation resistance standards ensures protection from electrical hazards.
- Environmental Impact Assessment
Environmental factors can influence wire properties. Standards may require assessments of the wire's performance under various conditions, such as temperature fluctuations, humidity, and exposure to corrosive substances. Compliance with these environmental tests ensures the wire maintains its performance and safety in diverse settings, prolonging its lifespan and reliability. This is critical in ensuring the long-term suitability of KPKuang wire in various operational environments.
In summary, adherence to safety standards related to KPKuang wire is not optional but essential. These standards encompass a range of crucial tests and assessments, ensuring the wire's safe and reliable performance in electrical systems. Meeting these standards safeguards personnel, prevents equipment damage, and protects the integrity of the overall electrical infrastructure.
Frequently Asked Questions about KPKuang Wire
This section addresses common inquiries regarding KPKuang wire, providing concise and informative answers to facilitate a clear understanding of its properties, applications, and safety considerations. These frequently asked questions and answers serve as a valuable resource for those seeking information on KPKuang wire.
Question 1: What is KPKuang wire, and what are its key characteristics?
KPKuang wire refers to a specific copper alloy designed for high-capacity electrical transmission and distribution. Key characteristics include high conductivity, exceptional tensile strength, and enhanced durability, making it suitable for demanding applications. The wire's precise composition, manufacturing process, and diameter control contribute to consistent performance.
Question 2: What are the primary applications of KPKuang wire?
KPKuang wire finds applications in high-voltage power transmission lines, substations, and industrial wiring systems. Its high conductivity minimizes energy loss in long-distance transmission, while its strength ensures reliability under mechanical stress. The wire's durability is critical for applications demanding prolonged service life.
Question 3: How does the manufacturing process impact KPKuang wire's performance?
The manufacturing process significantly impacts KPKuang wire's properties. Rigorous quality control during copper processing and wire drawing ensures consistent conductivity, tensile strength, and dimensional accuracy. These processes contribute to the wire's overall performance and reliability. Careful attention to detail in manufacturing is critical.
Question 4: What safety standards are associated with KPKuang wire?
Safety standards for KPKuang wire are crucial for ensuring reliable and hazard-free operation. These standards encompass electrical conductivity testing, tensile strength and elongation limits, and insulation resistance testing. Compliance with these standards safeguards against potential risks, including electrical shocks, fire hazards, and equipment damage.
Question 5: What are the factors influencing the durability of KPKuang wire?
KPKuang wire's durability is influenced by factors such as material composition, manufacturing processes, and environmental conditions. High-purity copper contributes to corrosion resistance, while precise manufacturing ensures consistent properties. Environmental factors like exposure to moisture and extreme temperatures also impact the wire's long-term performance. Careful consideration of these factors is crucial for predicting the wire's service life.
These FAQs provide a concise overview of KPKuang wire. Further information on specific applications and technical details can be found in the associated documents and resources.
The next section will explore the detailed technical specifications of KPKuang wire, including specific material compositions and manufacturing standards.
Conclusion
The exploration of KPKuang wire reveals a complex interplay of material properties, manufacturing processes, and application-specific requirements. High conductivity, exceptional tensile strength, and robust durability underscore the wire's suitability for demanding electrical applications. The careful consideration of wire diameter, insulation quality, and adherence to safety standards are paramount to ensuring reliable and safe electrical infrastructure. Manufacturing processes, from material selection to final testing, directly influence the wire's performance characteristics and ultimately its longevity. Understanding these intricate factors is crucial for selecting and deploying KPKuang wire effectively.
The consistent application of KPKuang wire, particularly in high-voltage transmission lines and intricate urban electrical grids, demonstrates its critical role in modern infrastructure development. The ongoing evolution of materials science and engineering techniques will undoubtedly refine KPKuang wire's performance, leading to even greater efficiencies and enhanced safety standards in the future. Maintaining rigorous adherence to safety protocols, informed by ongoing technological advancements, remains essential for the continued dependable operation of electrical systems incorporating this vital wire.
You Might Also Like
P Diddy's Impressive Career: What Does He Do?Yellowstone Star Lainey Wilson: Hot New Details!
Trisha Meili's Education: Degrees & Certifications
Greg Gutfeld's Wife: Meet The Mystery Woman Behind The Host
RIP P Diddy? Death Hoax Debunked!
Article Recommendations
- Crew Gaines Disability
- Who Is Brittany Underwood Check Out Her Latest Discovery
- How Did Aubreigh Wyatt Kill Herself
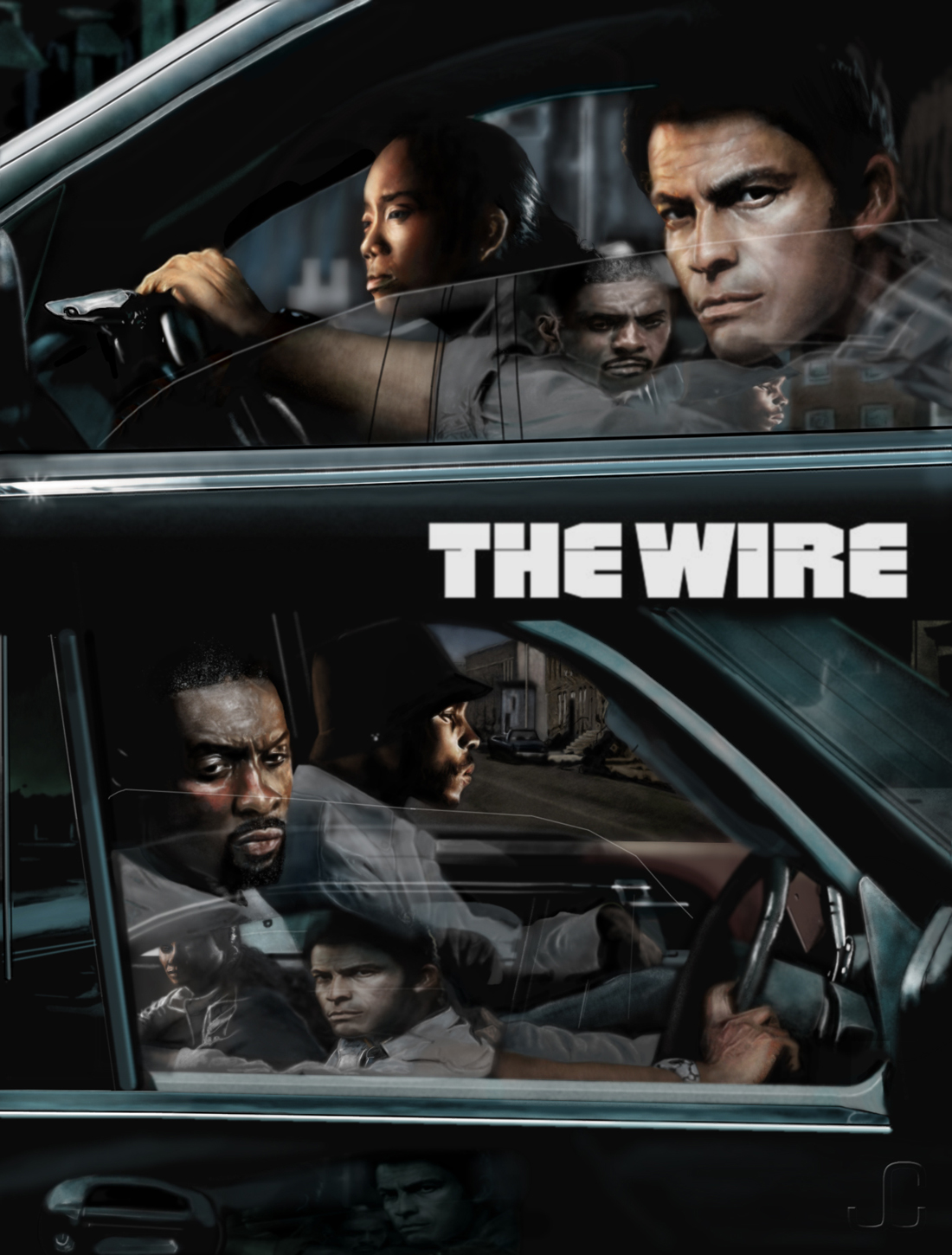

